Motor-driven systems account for nearly half of the electricity used in commercial and industrial facilities, according to the U.S. Department of Energy. Motors also break down frequently, and are costly to repair and replace. It’s no wonder then, that manufacturers are constantly trying to improve motor efficiency and performance. Here we highlight some innovative motor technologies.
Copper rotor motors
Copper rotor motors substitute copper for aluminum in the squirrel cage section of the rotor. Why copper? It’s far more conductive than aluminum, reducing rotor losses. Rotor losses typically account for 25% of total motor energy losses. Reduced electrical losses also reduce the amount of heat rejected into the motor enclosure. This means that a smaller cooling fan can be used, reducing friction and windings losses.
Copper rotor motors are now commercially available. A number of manufacturers have introduced ultra-efficient die cast models.
Permanent magnet motors
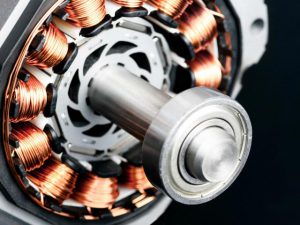
Conventional asynchronous induction motors can be designed for low operating speeds, but efficiency and power factor tend to drop. Permanent magnet (PM) synchronous motors provide high efficiency, low speed and high torque in a single unit.
PM motors use powerful ceramic or rare earth magnets attached to the rotor to establish a permanent magnetic field. This design significantly reduces the secondary circuit rotor losses associated with the aluminum rotor cage of conventional induction motors.
PM units are designed for variable speed operation. They must be controlled by an inverter or variable speed drive specifically designed for operation with a permanent magnet design. Permanent magnet units provide a high power factor and they exceed premium efficiency standards.
A recent development is the use of a conical geometry on both ends of the rotor/stator, which maximizes surface area and allows use of inexpensive ferrite magnets. Another new PM motor design incorporates an integrated and configurable variable speed drive onto the exterior circumference of the motor, resulting in a very compact and slim profile. Another trend is printed circuit board stators that replace wound wire stators which reduces motor weight by 60%.
Applications for PM systems include adjustable speed pumps and fans, as well as mixers, conveyors and printing presses.
Switched reluctance motors
Switched reluctance (SR) synchronous motors have rotors without magnets, bars or windings. The rotor is basically shaped iron laminates. SR rotor poles remain static, unlike the bars on a squirrel cage induction rotor, which change constantly. Only two pair of rotor poles ever line up with two pair of stator poles. So, energizing a different pair of stator poles causes the rotor to rotate in order to line up again.
An SR drive system requires an electronic power converter to control torque and speed. It can’t be used with a conventional variable speed drive. SR motors are often used in air-conditioning compressors, as well as industrial applications, such as blowers and high-speed pumps.
SR motors offer a number of benefits including high efficiency, variable speed capability low cost and flexibility — they’re available in a variety of shapes and sizes. SR motors are rugged and simple in construction, although they do have high vibration and noise levels. The need for a controller is also a potential downside.
Which type is right for your application?
Copper rotor motors can replace conventional induction units in almost any general motor application. Consider PM and SR motors when the application requires speed control, operates more than 2,000 hours a year and involves frequent stops and starts.
See Motor Systems from the U.S. Department of Energy for more tips and resources for improving motor efficiency.