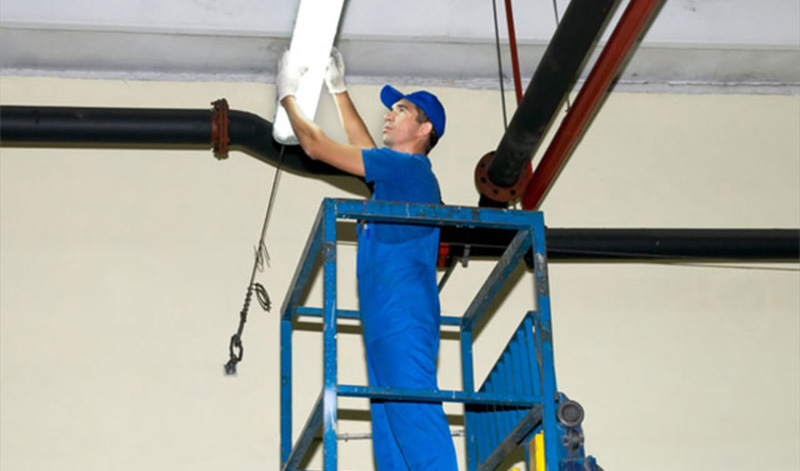
Lighting System Maintenance: Savings and Performance
Let’s talk about lighting maintenance. Lighting makes up about 20% of total energy use in the average commercial building, according to the U.S. Department of Energy. At the same time, lighting is critical to a safe and comfortable indoor environment.
Given the importance of good lighting and the need to reduce operating costs, a detailed plan to optimize lighting performance and efficiency should be a high priority. Often, however, lighting maintenance doesn’t extend beyond replacing burned-out bulbs. An effective maintenance policy that includes written procedures, training and inventory control can improve light output and save you money.
Focus on the basics
Maintenance is the most overlooked, yet cost-effective way, to reduce the overall cost of lighting. Light levels decrease over time because of aging light fixtures and the dust that collects on lamps. Together, these factors can reduce total illumination by 50% or more while light fixtures continue to draw full power. Often, facilities compensate for this light loss by adding more fixtures, which increases energy costs.
The following maintenance strategies can help improve lighting system performance:
- Clean fixtures, lamps and lenses every six months.
- Replace lenses if they appear yellow.
- Clean or repaint indoor walls regularly; dirt collects on surfaces, reducing the amount of light they reflect.
- Use group lamp replacement, which saves labor and optimizes light levels.
Consistency is the best policy
A lighting maintenance policy serves as a guideline for consistently applying best practices for reducing costs and optimizing system performance. The following are some basic elements that should be included in an effective policy:
- Specifications for all lighting equipment, as well as vendor and service provider contact information
- Procedures for replacing and cleaning fixtures, including a schedule with a service tracking log
- Schedule for adjusting controls
- Procedures for lamp and ballast disposal
To maximize energy savings, coordinate the lighting policy with your overall energy management strategy. Review your policy when considering a lighting upgrade.
Shed some light
Training is critical to carrying out an effective lighting maintenance policy. Educate appropriate staff members on procedures, such as cleaning, lamp and fixture replacement, and fixture inspection. Include a detailed overview of the written maintenance policy and each employee’s role. Provide regular updates to account for new technologies, policy changes or staff turnover.
Think group replacement
Spot replacement (replacing lamps as they burn out) is the most commonly used technique in traditional maintenance programs. While group replacement can increase initial lamp costs, it offers several advantages:
- Optimized light levels. In most lamps, light output depreciates over time, reducing overall light levels before they fail.
- Energy savings. Group replacement integrates easily with efficiency upgrades, potentially reducing energy costs.
- Lower maintenance costs. Group relamping can be performed by outside contractors, potentially reducing the size of an in-house maintenance staff.
Lamp and fixture compatibility is another factor to consider. Matching replacement lamps to existing fixtures and ballasts can be tricky, especially with older fixtures. Installing new fixtures made for new lamps produces superior energy savings, reliability and longevity when compared with spot relamping.